What is PVD Coating? It’s Like a Superhero for Your Metal!
So, let’s dive into the world of PVD coating, shall we? Picture this: you have a shiny piece of metal that looks like it just came off the assembly line. But wait! You want it to be more than just eye candy; you want it to be durable, resistant to wear and tear, and maybe even look cooler than your neighbor's new car. Enter PVD coating – the superhero of surface treatments!
PVD stands for Physical Vapor Deposition (yes, I know it sounds fancy). It’s a process where materials are vaporized in a vacuum and then deposited onto the surface of an object. Think of it as giving your metal that ultra-glam makeover without all the drama of reality TV. Who wouldn’t want that?
The Science Behind PVD Coating: Not Rocket Science… But Close!
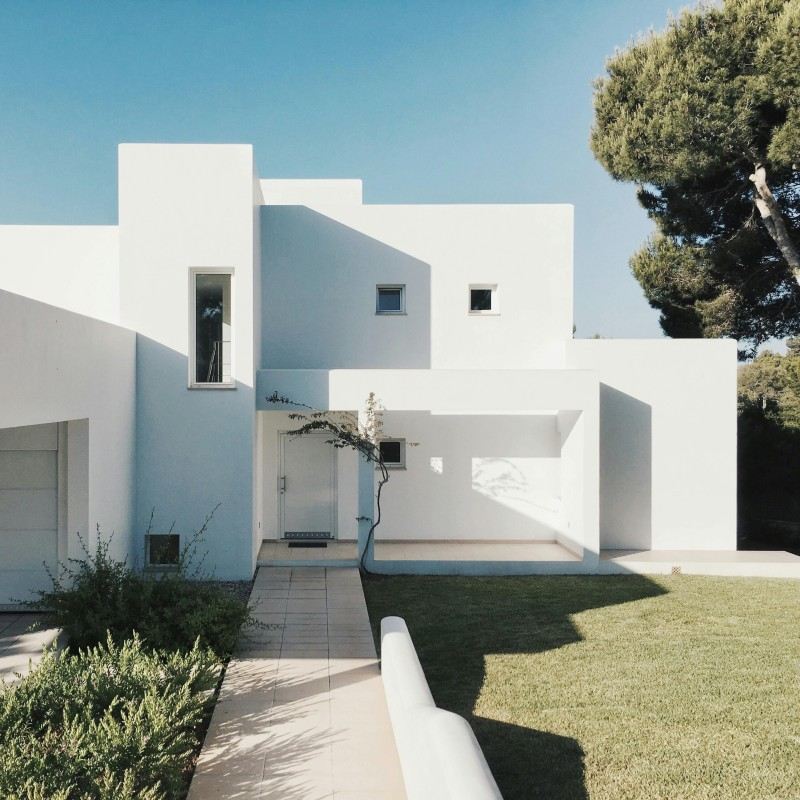
Now, I can hear some of you yawning already at the mention of science. But hang on; this isn’t your high school chemistry class! The beauty of PVD coating lies in its ability to create a thin layer (we’re talking microns here) that bonds tightly to the substrate material. This means better adhesion and durability—like super glue but way cooler!
But how does this magic happen? Well, during the process, materials such as titanium or zirconium are heated until they turn into vapor (cue dramatic music). This vapor then condenses on your metal surface like morning dew on grass. Voila! You’ve got yourself a shiny new finish that can withstand scratches, corrosion, and even some harsh chemicals.
Different Types of PVD Coating: Choose Your Fighter!
Did you know there are different types of PVD coatings? It's like picking your favorite ice cream flavor; each one has its unique characteristics! Here are a few popular types:
- Titanium Nitride (TiN): The classic choice—it gives metals a gold-like appearance and is known for its hardness.
- Zirconium Nitride (ZrN): A little less common but equally impressive with its golden hue and excellent wear resistance.
- Aluminum Titanium Nitride (AlTiN): This one's like the overachiever—great for high-temperature applications.
- Chromium Nitride (CrN): If you're looking for something with great corrosion resistance while maintaining a sleek look, CrN is your go-to!
So which one do you think would suit your needs best? Or are you still stuck on deciding between chocolate chip or mint chocolate chip?
Applications of PVD Coating: Where Can You Use It?
Alright folks, let’s talk about where you might find this magical coating in action because trust me—it’s everywhere! From kitchen knives that slice through veggies like butter to aerospace components enduring harsh conditions up in the sky—you name it!
PVD coatings are also used in medical devices because who wants bacteria hanging out on their surgical tools? Not us! And don’t forget about watches and jewelry; they get their bling from these coatings too! So next time someone compliments your shiny watch, just nod knowingly—they have no idea about the science behind it!
PVD Coating Applications in Electronics and Optics
Now let's take a closer look at how PVD coating is making waves in the electronics and optics sectors. This technology is not just limited to traditional applications; it's evolving rapidly! For instance, in the semiconductor industry, PVD coatings are utilized for thin film transistors and capacitors. They improve conductivity and reduce defects, making them essential for modern electronics.
In optical applications, anti-reflective coatings and mirrors are enhanced with PVD technology, leading to better light transmission and durability. Additionally, display technologies such as touch screens and OLED displays benefit from improved image quality and touch sensitivity thanks to these coatings. Solar cells also see advancements with thin-film solar panels made possible by PVD coatings, boosting efficiency while lowering production costs.
Application Area | Specific Use Cases | Benefits |
---|
Semiconductors | Thin film transistors, capacitors | Improved conductivity and reduced defects |
Optical Coatings | Anti-reflective coatings, mirrors | Enhanced light transmission and durability |
Display Technology | Touch screens, OLED displays | Better image quality and touch sensitivity |
Solar Cells | Thin-film solar panels | Higher efficiency and lower production costs |
LEDs | LED chips and packaging | Improved brightness and energy efficiency |
This table summarizes various application areas of PVD coating in electronics and optics along with their specific use cases and benefits. It’s clear that PVD technology is paving the way for innovation across these industries.
PVD Coating Technology Advancements: The Future is Bright!
The advancements in PVD coating technology are nothing short of exciting! With material innovations leading to new alloys and compounds being developed, we’re seeing increased performance across various applications. Process optimization is also at play here—improved deposition techniques mean higher throughput and lower costs.
The integration of AI and robotics into manufacturing processes enhances precision while reducing human error. Not to mention the focus on environmental sustainability—reducing waste and energy consumption is becoming a priority for many companies in the industry.
Advancement Area | Description | Impact on Industry |
---|
Material Innovation | Development of new alloys and compounds | Increased performance and application range |
Process Optimization | Improved deposition techniques | Higher throughput and lower costs |
This table highlights some key advancements in PVD coating technology along with their descriptions and impacts on the industry. As we continue to invest in research and development, we can expect faster innovation cycles leading to new applications that will further enhance our everyday lives.
Benefits of PVD Coating: Why Should You Care?
Now let’s get down to brass tacks—why should you care about PVD coating anyway?
- Durability: Increased lifespan means fewer replacements—more money saved!
- Aesthetics: Available in various colors; say goodbye to boring metallic finishes.
- Environmentally Friendly: Unlike some other coatings that use harmful chemicals, PVD is generally safer for Mother Earth.
- Versatility: Works on many substrates—from metals to plastics—making it suitable for countless applications.
What do you think—isn't it time we start appreciating our coated friends more?
Conclusion: Embrace Your Inner Geek with PVD Coating
In conclusion (yes, we made it!), if you're looking for an upgrade for any metal surfaces in your life—or if you're just curious about how things work—consider exploring PVD coating further. It truly is like giving metal superpowers while keeping things stylish at the same time!
So whether it's knives in your kitchen or parts in machinery, remember—the right coat can make all the difference! And hey, next time someone asks what makes those surfaces so special, drop some knowledge bombs about PVD coating—they’ll be impressed!